New project alert!!! Manchester House!
- Kushner Studios
- Nov 8, 2024
- 1 min read
Our current project, an unbuilt 1,400-square-foot home in New Hampshire, will be the state’s first 3D-printed house. This innovative venture is a collaborration between our firm and Madco3D, focusing on their Hybrid House™ concept. By leveraging 3D printing technologies, we aim for faster construction times, greater design flexibility, and enhanced environmental sustainability.
Despite its modest scale, this project has the potential to make a significant impact on affordable housing both in New Hampshire and beyond. We’re excited to be at the forefront of this growing movement, where are collaborative use of TAM’s robotic technology and Sika USA’s new mortar, exemplifies a forward-thinking approach to construction.
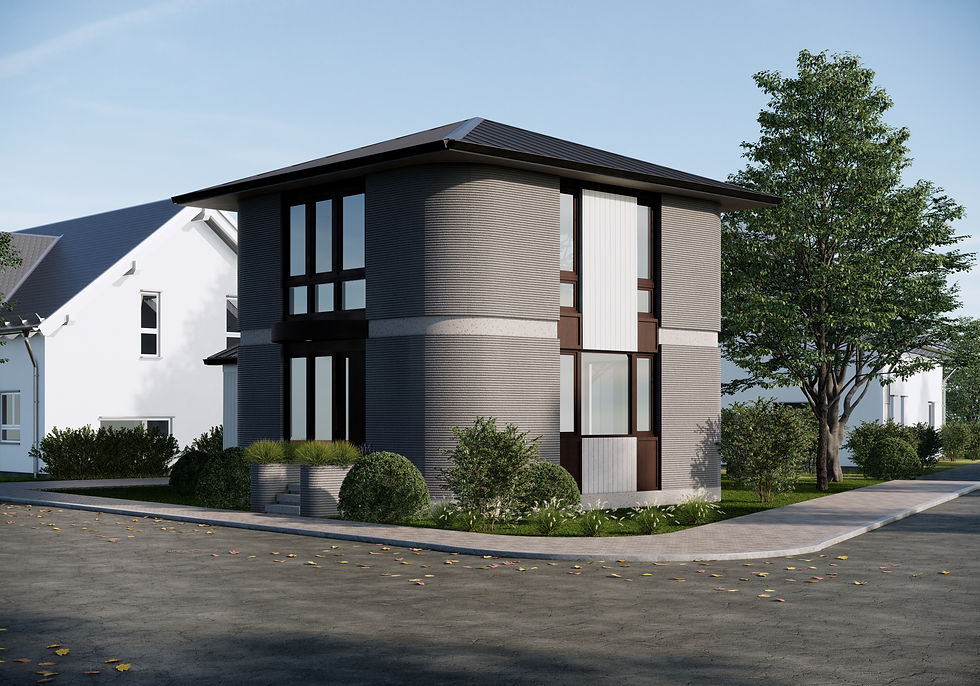
Beyond their immediate Project, Madco3D innovation has led to considerable demand, with requests for over 100 houses within the state alone. While costs vary based on the home’s style and size, Madco3D emphasizes that their 3D-printed homes will remain within the affordable housing price range. In areas where additional materials like wood are required (for example, window casings, doors and moldings), Madco3D prioritizes upcycled materials wherever possible.
Madco3D’s work goes beyond housing. The company is actively engaged in environmental conservation efforts; such as, partnering with the university of New Hampshire (UNH) and other organizations to rebuild coral reefs worldwide. Their collaboration with UNH’s John Olson Advanced Manufacturing Center provides internships to students specializing in civil and mechanical engineering, allowing them hands-on experience in 3D printing and design.

Through this project and others, Madco3d is helping to pave the way for a sustainable future in construction, addressing critical needs in affordable housing, and environmental resilience.
Comments